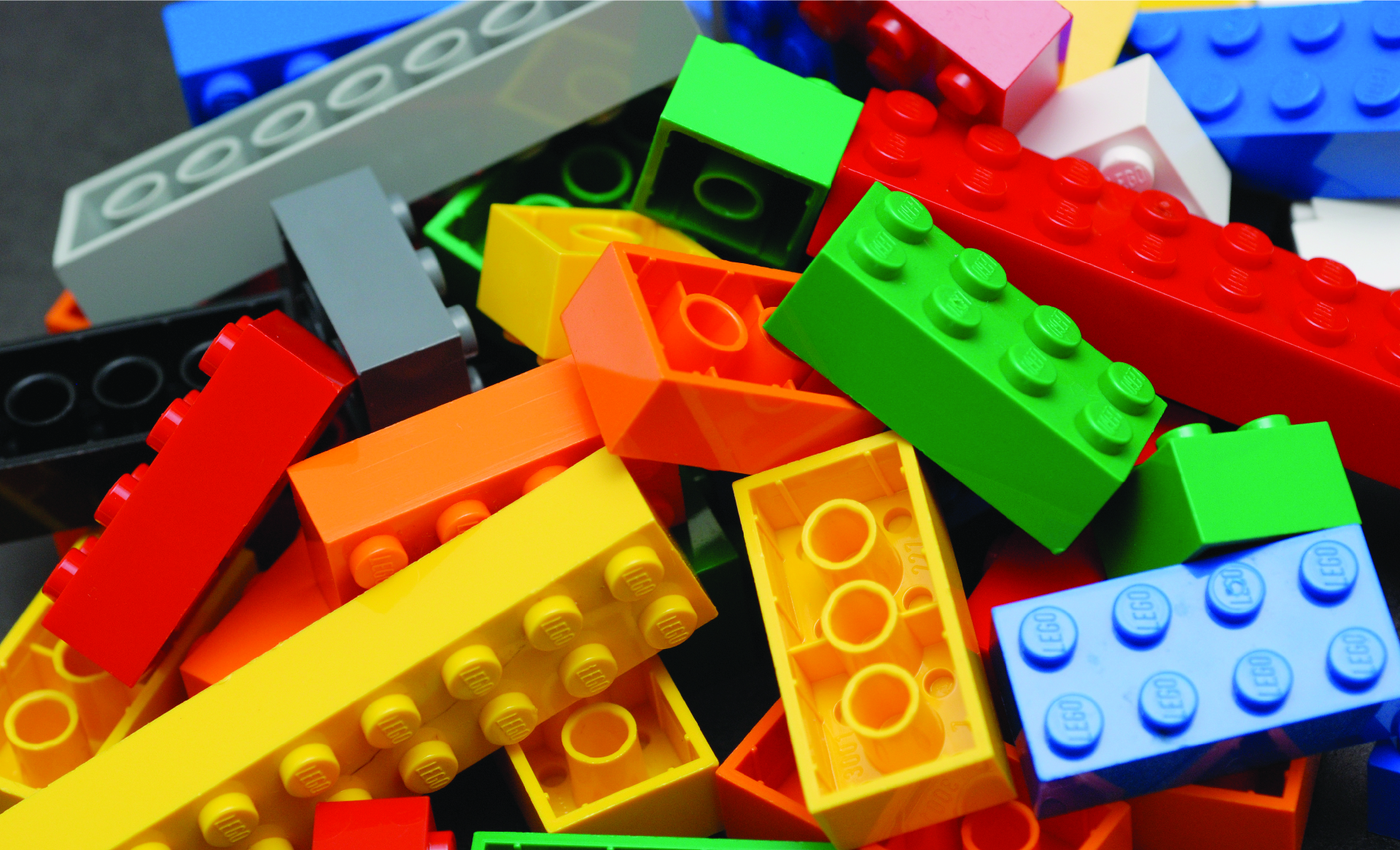
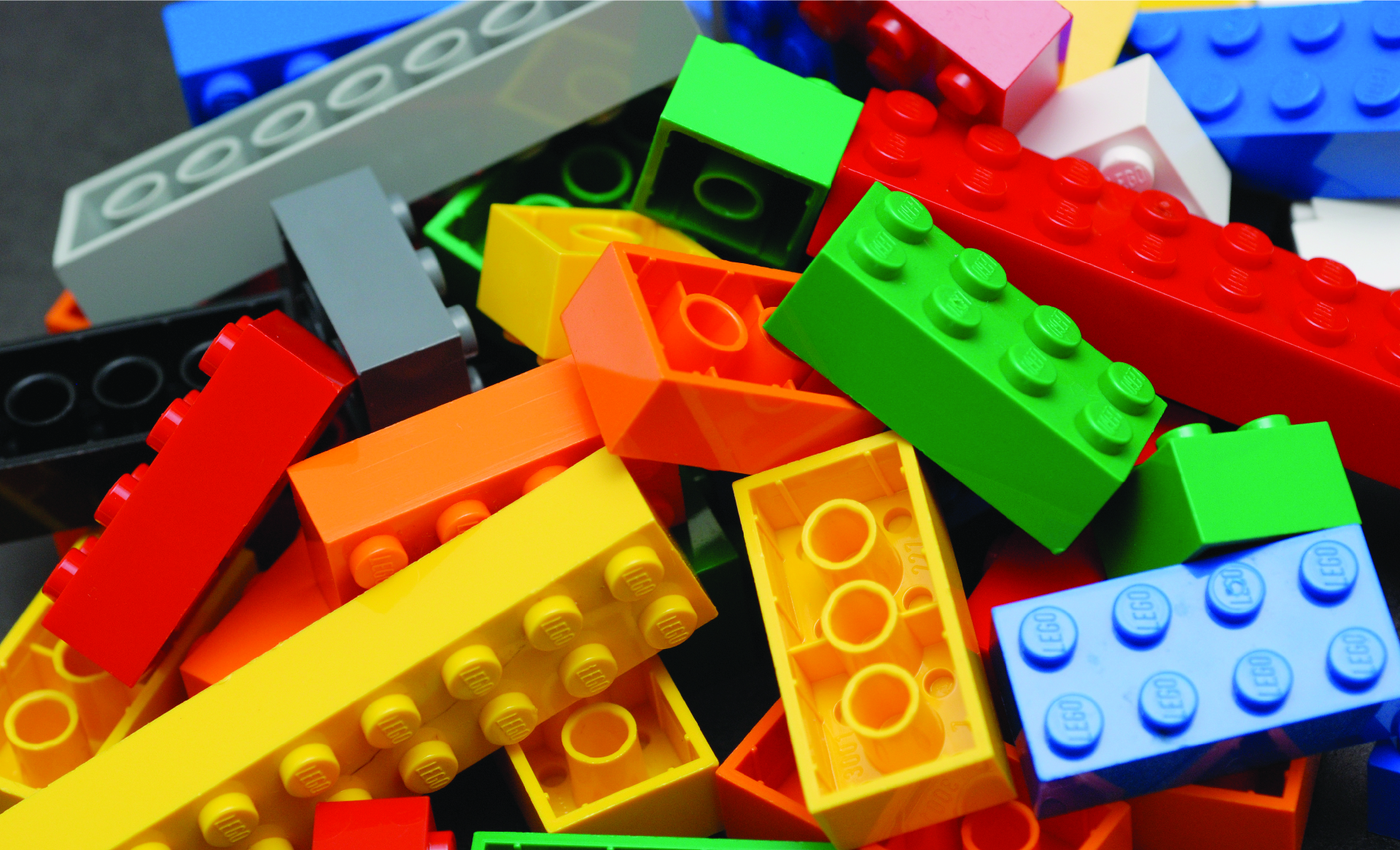
Last week I visited the new Factory OS modular manufacturing facility on Mare Island in Vallejo. The tour re-ignited my interest in this production approach. (We did a modular housing project in Sunnyvale in 2015. There were a “Series of Unfortunate Events” on that project that left a bad taste in my mouth). Nevertheless, as building costs continue to rise, prompting protracted “value engineering” exercises during development and into construction, I am convinced there must be a more intelligent way to find economies. If you are reading this – I suspect you agree. If you are mulling over modular, puzzling about prefab or trying to figure out factory-built - here are 7 things you need to consider before you leap.
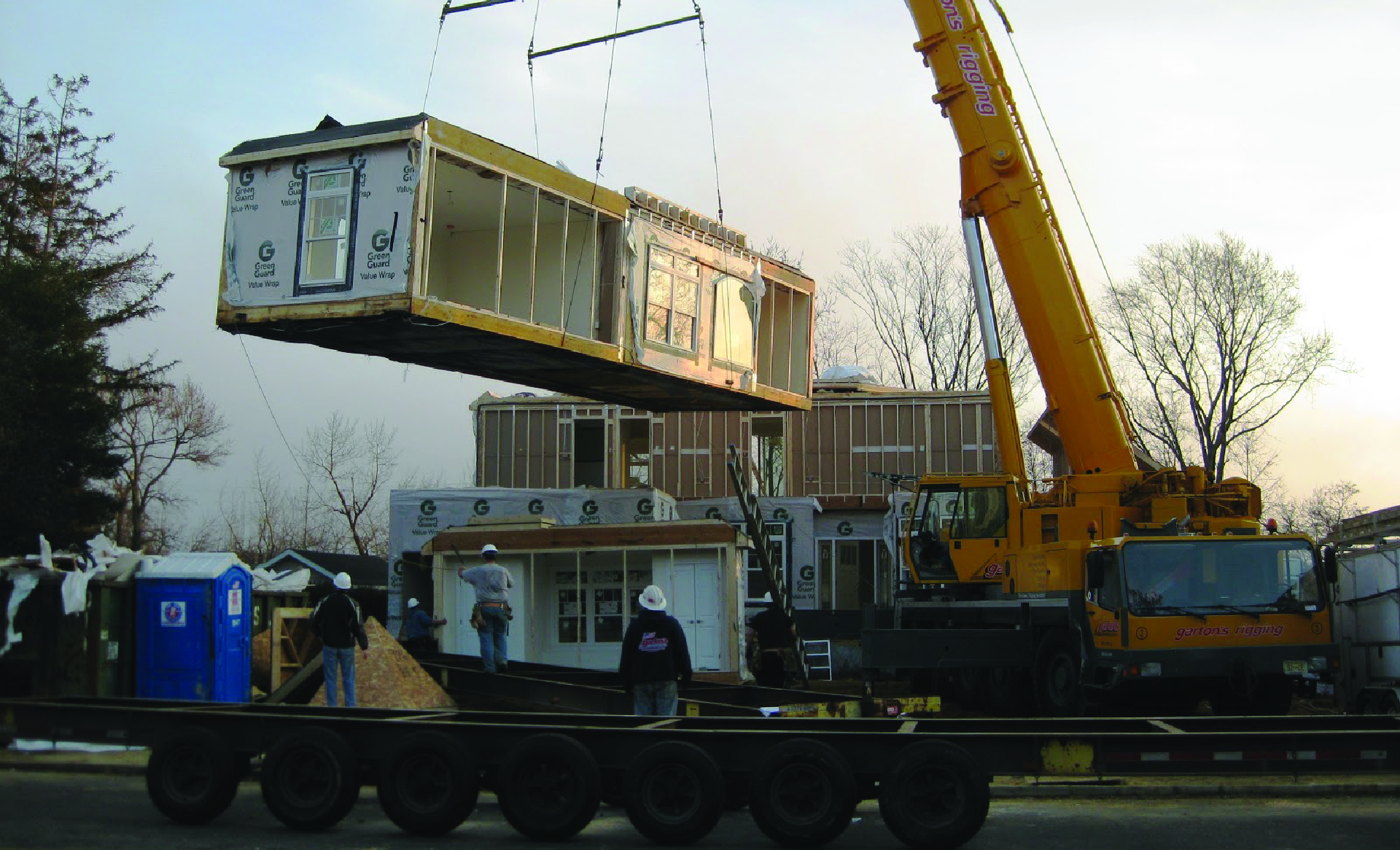
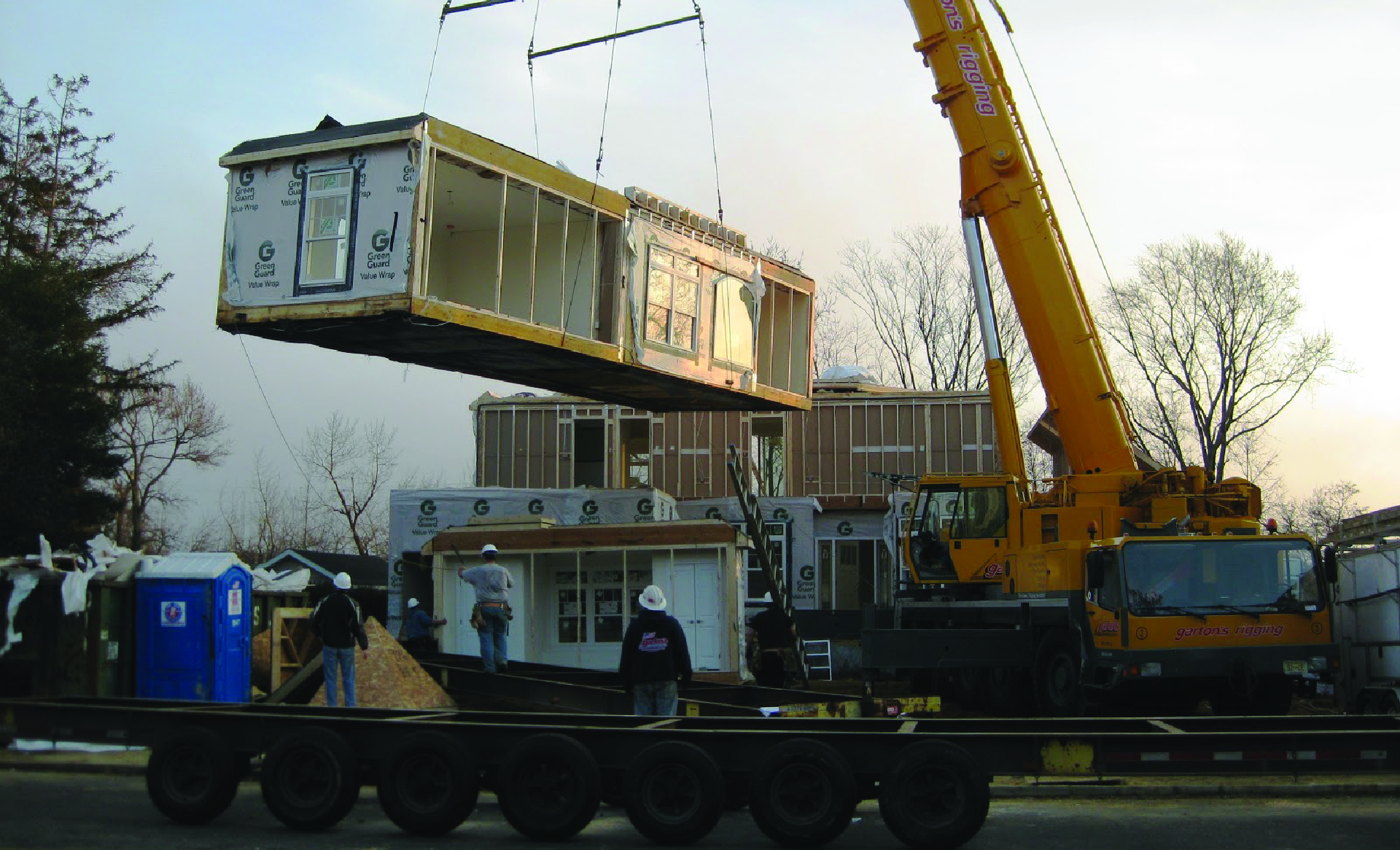
Image above - Understanding the critical dimensions of the modules is Task #1
1. Dimensions matter – Understanding the limitations of what fits on the back of a semi-trailer and how it rolls from factory to site is critical. We have had clients who half way into a project announce that they want to explore modular... only to realize that the units as designed wouldn’t neatly fit into the factory “mold”. Widths, lengths and heights, along with how modules will be joined, clad and roofed on-site, all need to be determined near the beginning of the design process.
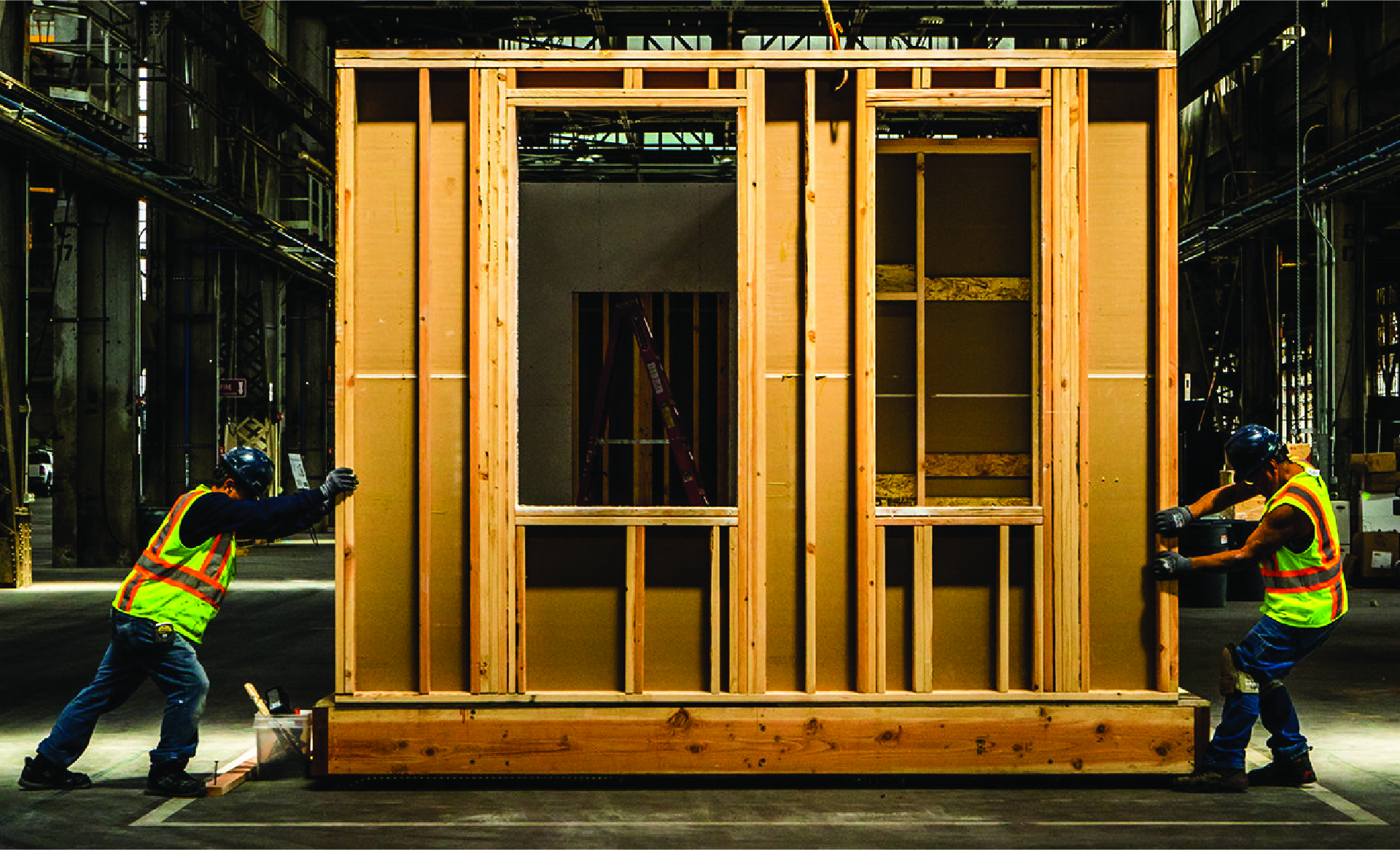
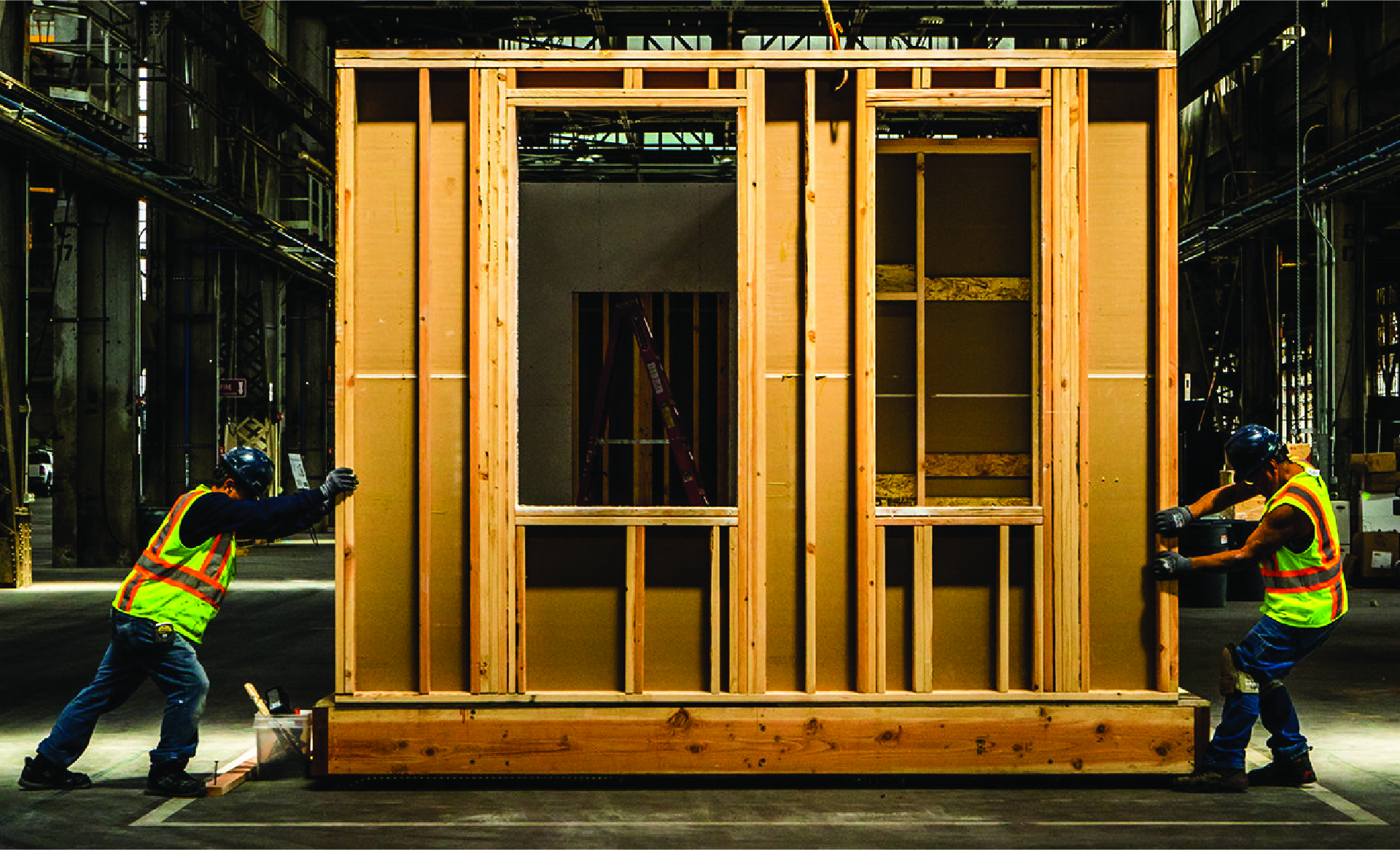
Image above - Modules are a product pre-assembled in a factory - and shipped to your site
2. Getting your approvals – When you build a modular unit, you (the developer) are purchasing a product. It's not too different than purchasing a refrigerator or dishwasher. As such, you will be required to obtain a permit from the State, in addition to the typical building permit from the local City or County. The state permit insures that the “product” (module) was constructed safely and soundly, and that it is fit for installation into your project. This requires a second set of permit documents and fees (of course). And some additional time in your pre-construction schedule. Plan accordingly.
Image above - Parkview Terrace, designed by Studio E Architects and built by Cahill Contractors is a modular project in Sunnyvale, CA
3. Choosing your team – Although designing and building a modular project is not rocket science, it does have a few quirks. A developer would be wise to enlist the help of a few team members who have been here before. (If this sounds like a shameless plug – it is.) The developer would also do themselves a favor by meeting with the City or County building department as early as possible. Many jurisdictions have yet to plan-check and inspect a modular build. They will have lots of questions. You and your team should have lots of reassuring answers.
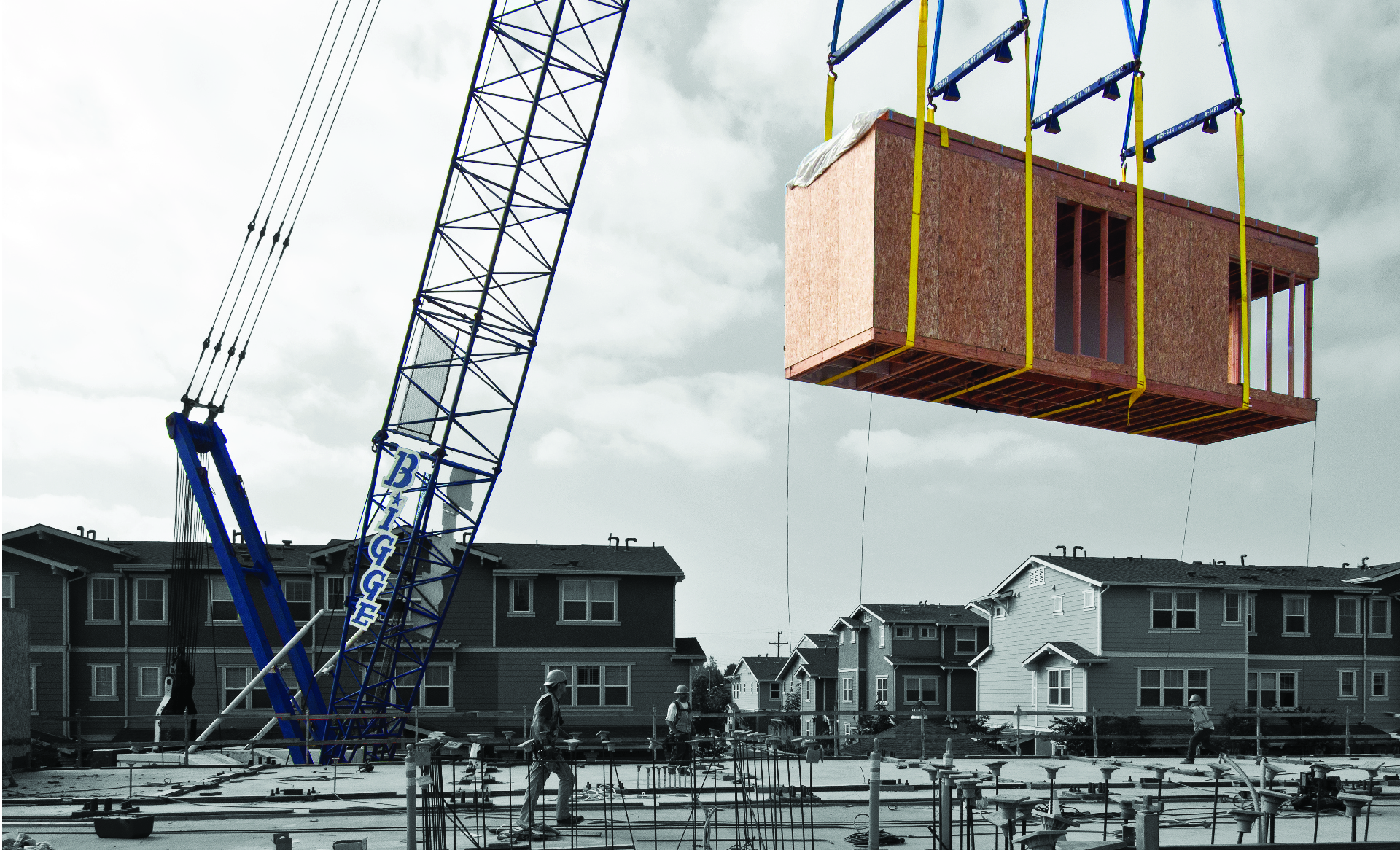
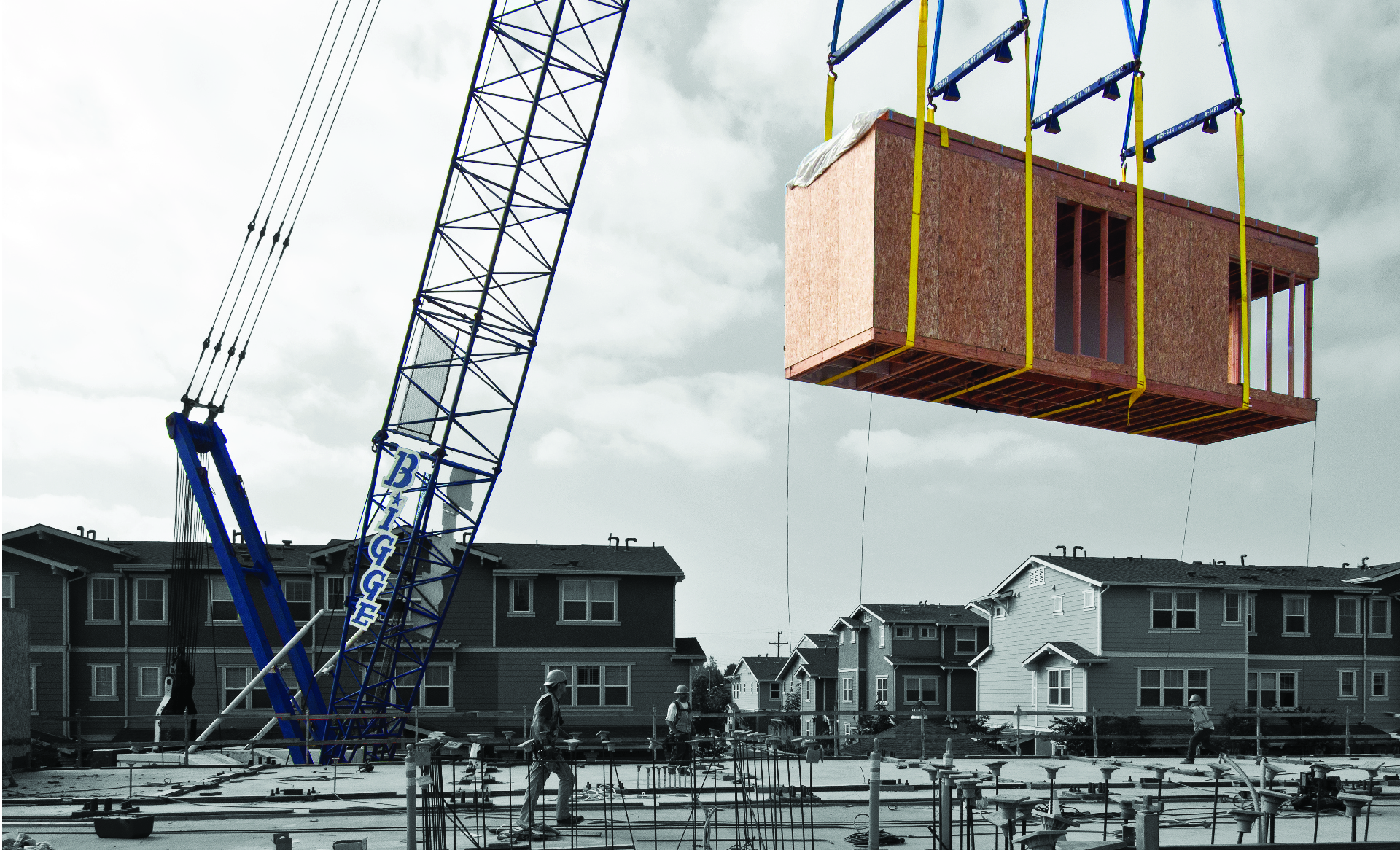
Image above - Most manufacturers claim that they can set 7-8 boxes per day during construction
4. It’s Time not Money – The important thing to know right up front about modular construction is that it will save time, not costs. If someone tells you otherwise – they are fibbing. Savings are realized by paying fewer months of interest on your construction loan and general contractor’s overhead. The factory-built boxes themselves cost more per volume of space than a stick-built unit.
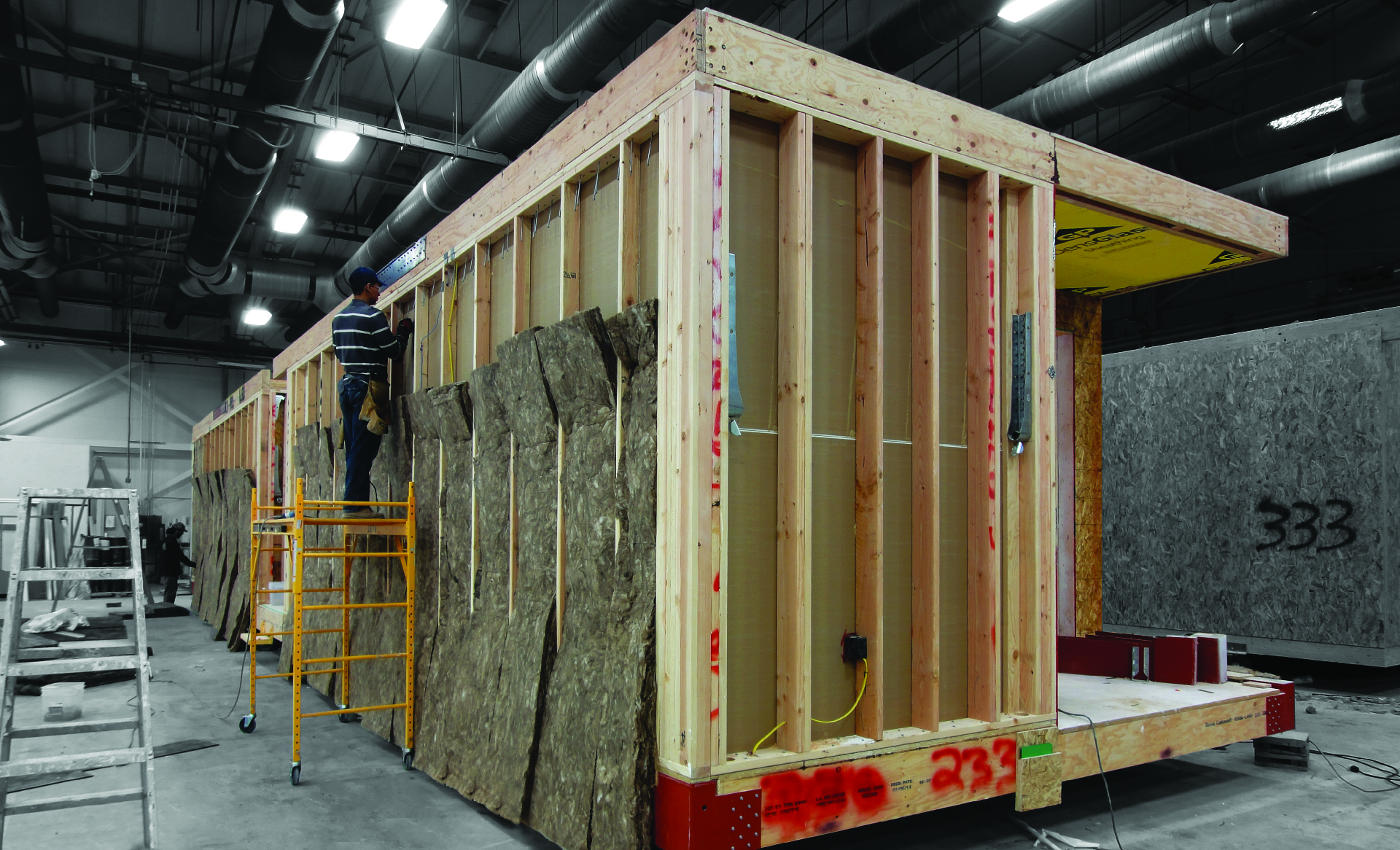
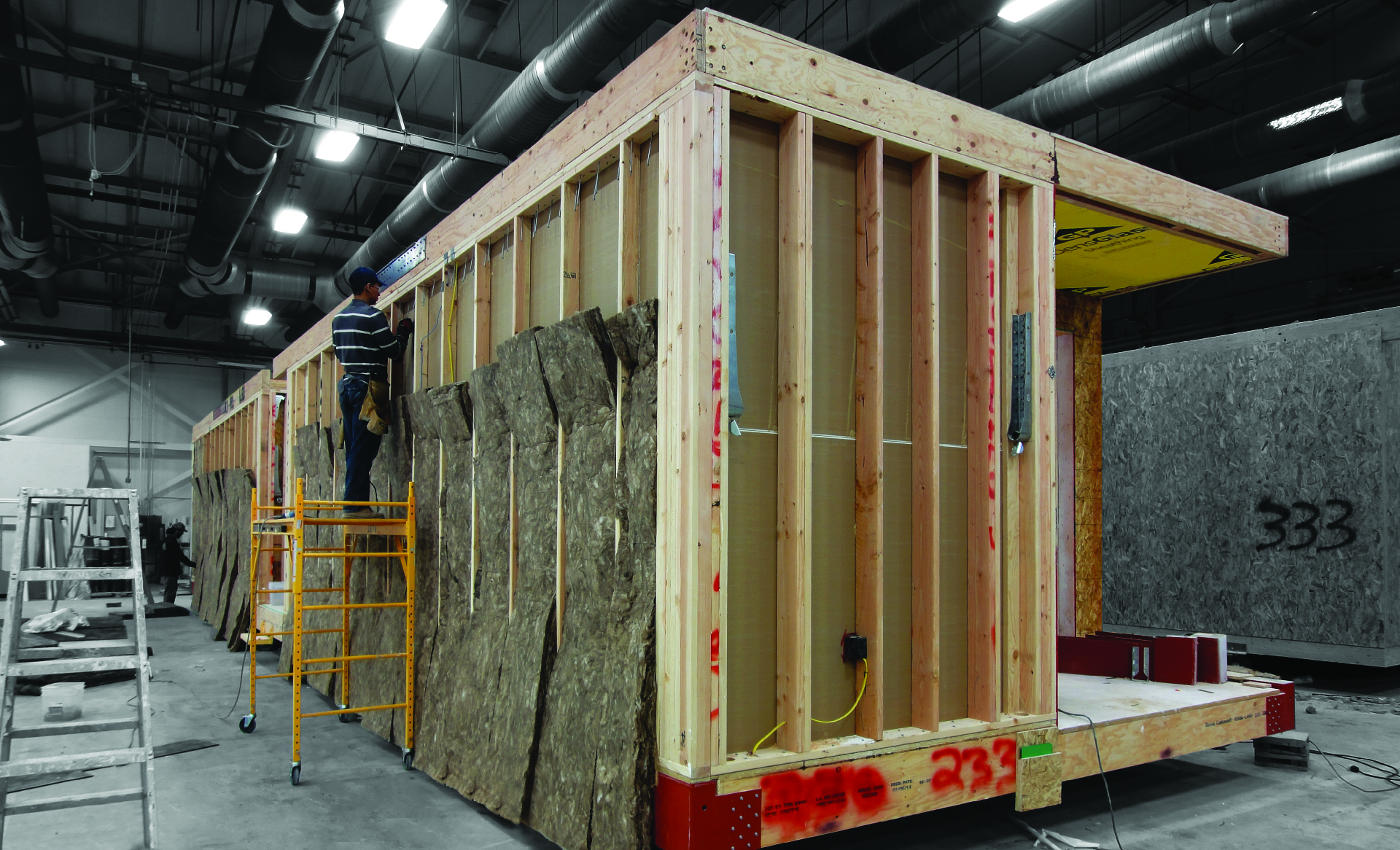
Image above - The six-sided box being built on the factory floor
5. Scoping the work – A clear understanding among your design team, general contractor AND modular manufacturer about who is responsible for what is essential. Overlapping scopes of work, or worse yet, no one taking on a task, will result in costly delays and change orders.
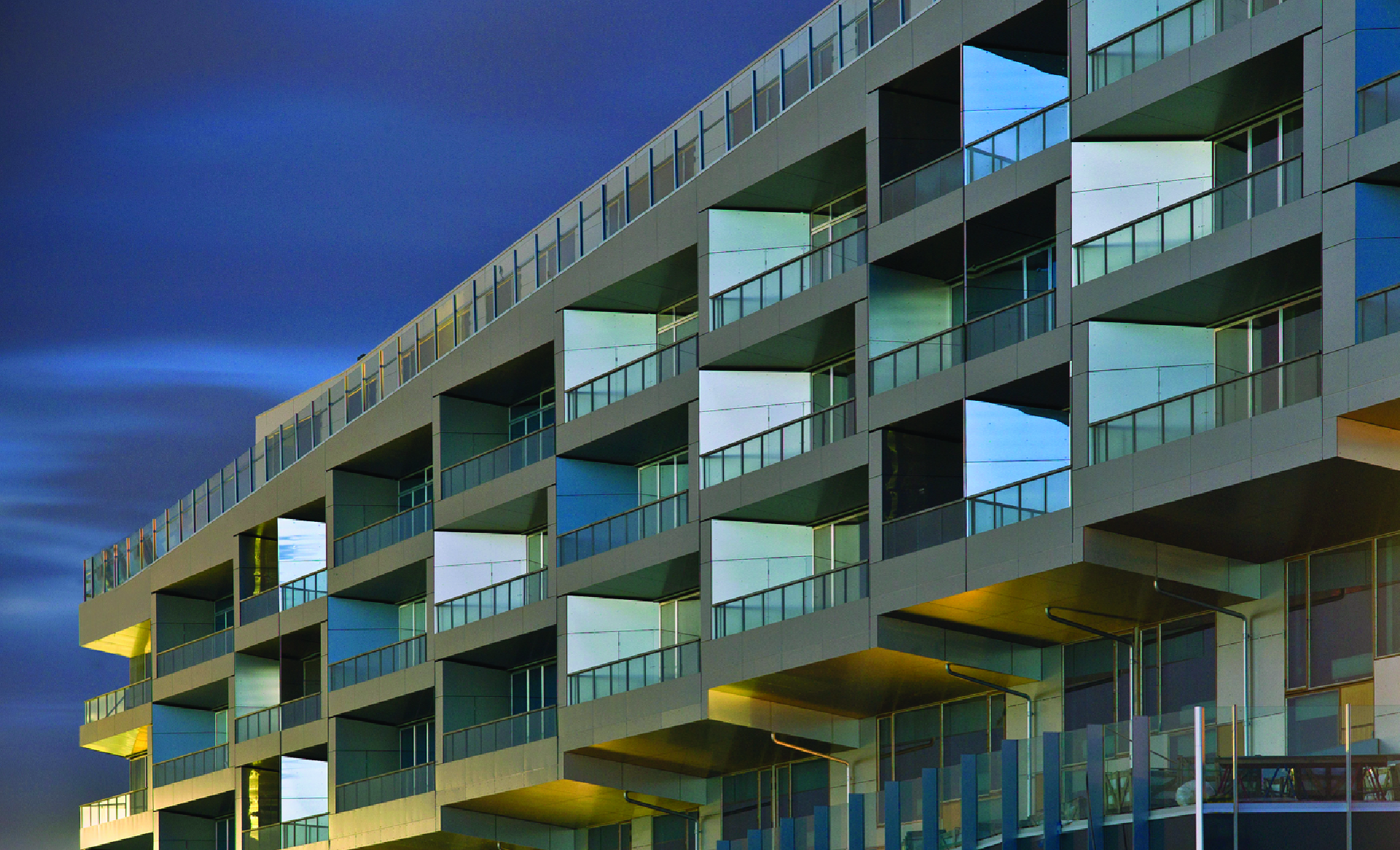
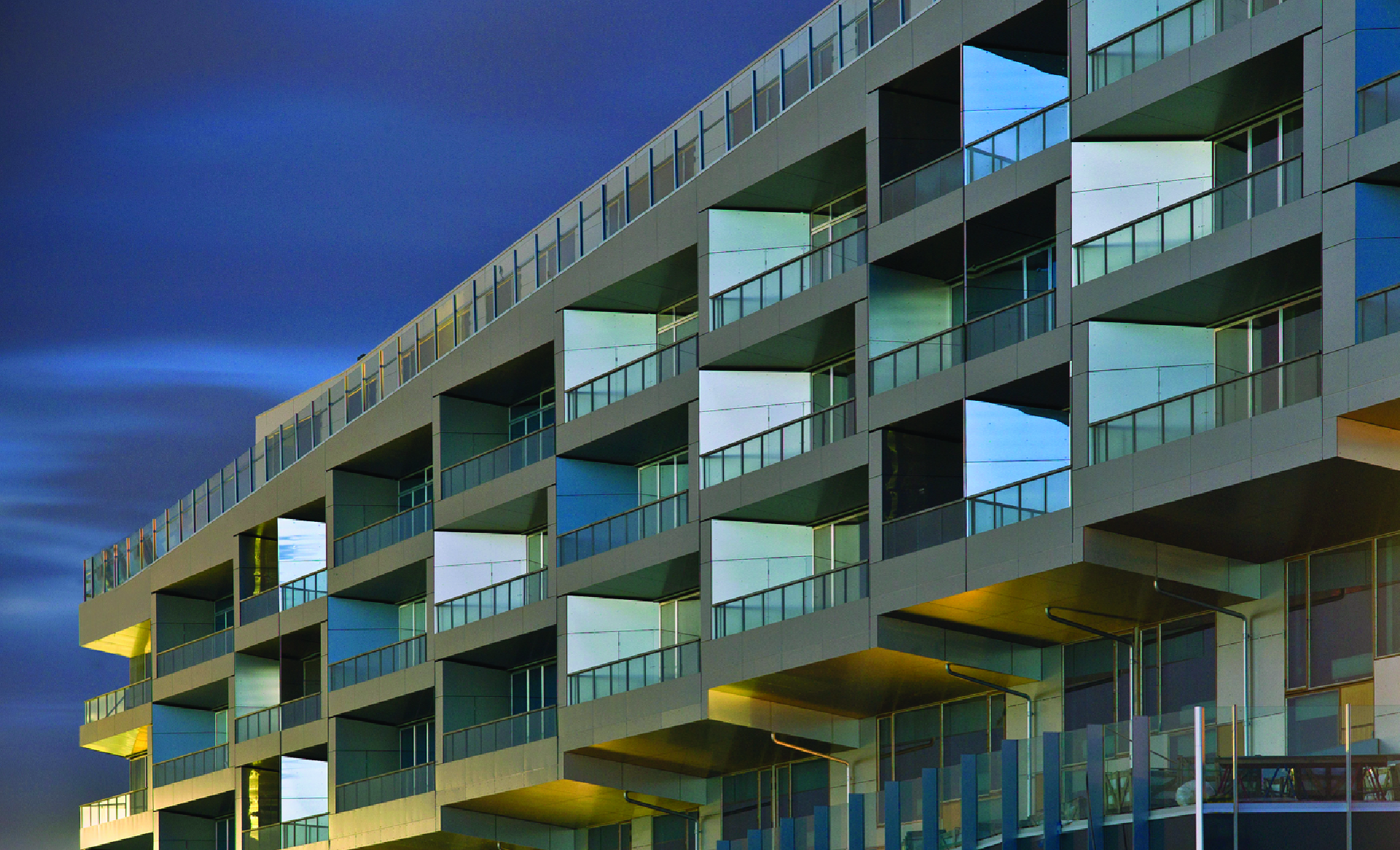
Image above - The Dream - Shiny bright modules set in perfect order - quickly and efficiently
6. Making deposits – This is the part of the process that makes the banks nervous. Modular manufacturers require large up-front deposits to get underway. Banks like to see materials on site (or in a warehouse) and tend to operate on a pay-as-you-go basis. Working with a lender who has done modular would be a great advantage. Short of that, a meeting between the bank and manufacturer is highly encouraged.
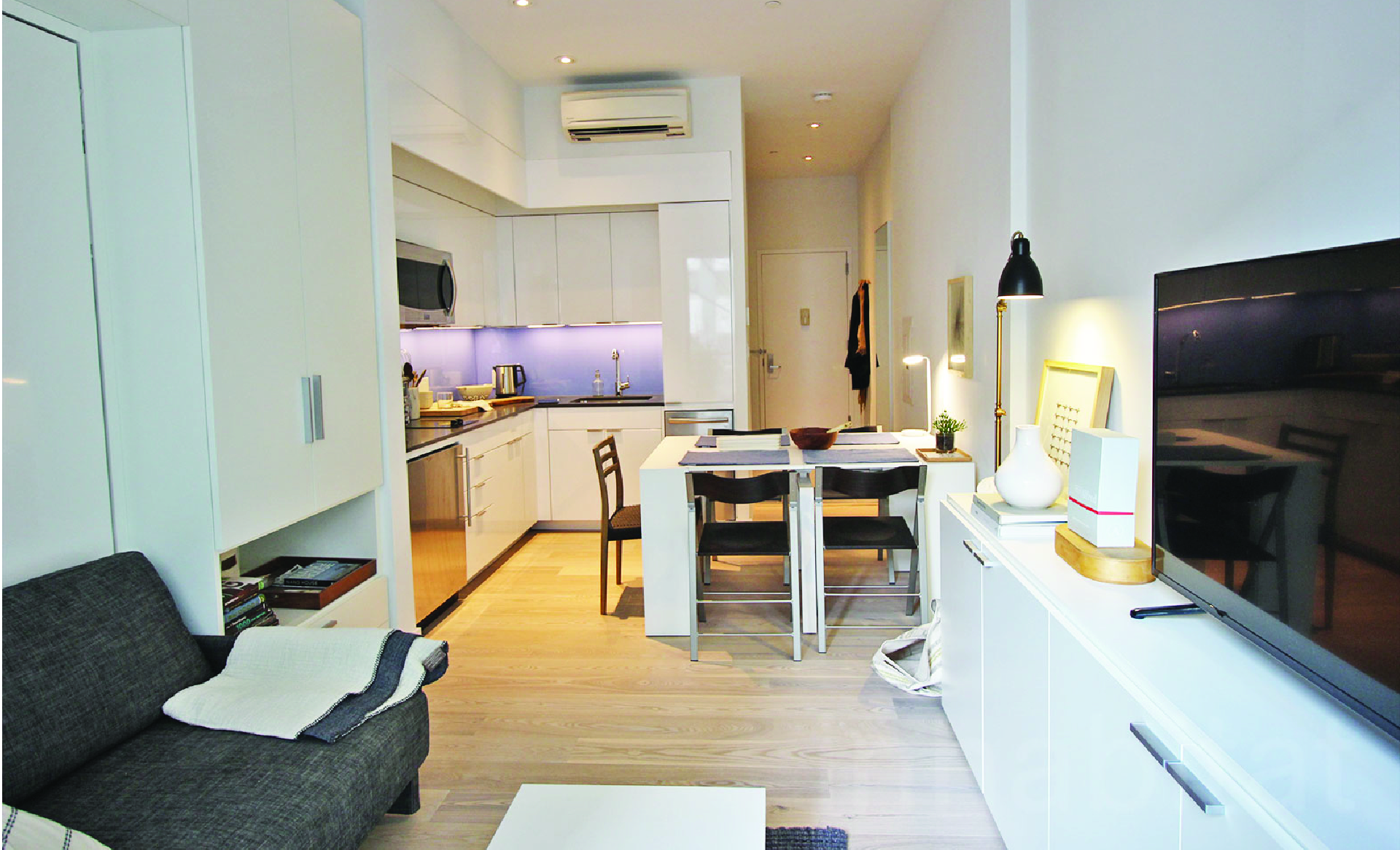
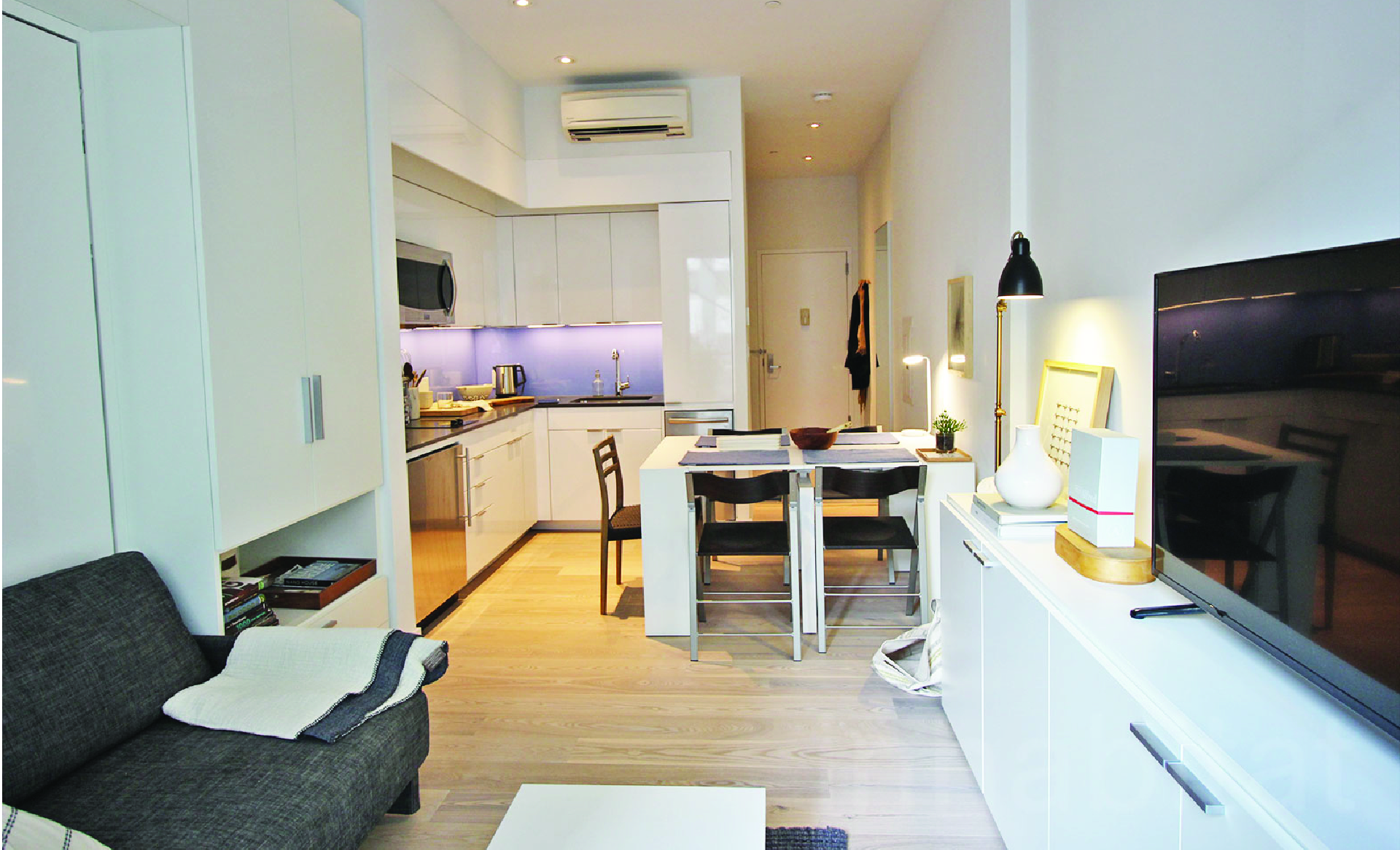
Image above - Modular units arrive on-site with all finishes and appliances installed
7. Who ya gonna call? – When a pipe breaks or an air conditioning unit doesn’t work or there’s a squeak in the floor – who do you call to inspect and repair/replace? Understanding what the modular manufacturer is responsible for vs. the general contractor will ease heartburn later. Make sure to ask about warranties on things like appliances that come installed in the shipped modules. Warranties on those begin from start of purchase, which may be 12 to 18 months ahead of Certificate of Occupancy. In other words – your warranties may be expired before your tenants reheat their first TV dinner.
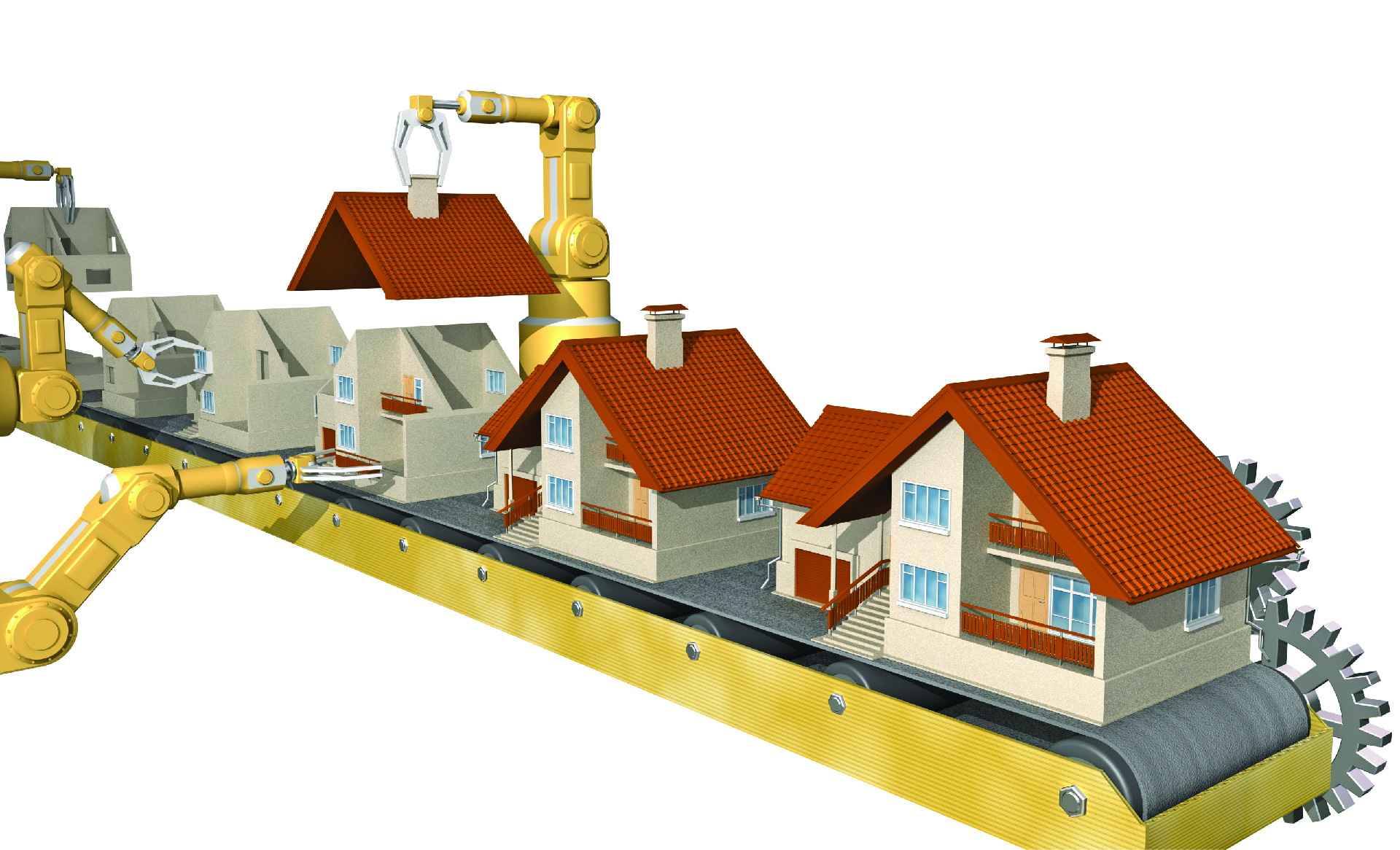
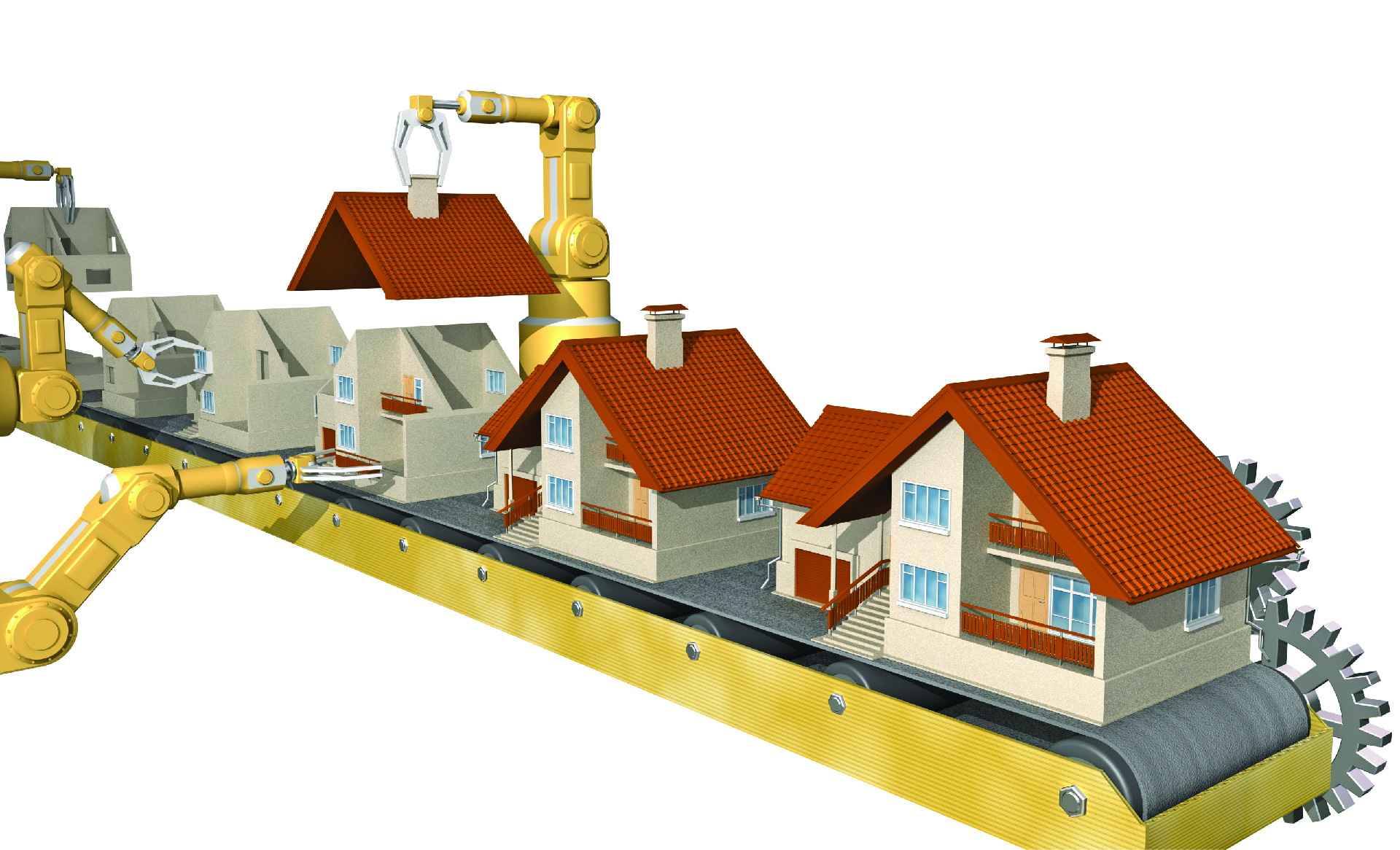
Someday soon (probably very soon) modular wood frame construction will be the way most multifamily and low-rise hospitality is built. Someday robots will be churning out high-quality factory-built housing (they are already starting to in Sweden). Someday banks will understand the system and general contractors who have done this type of work will be commonplace.
Until then – proceed with caution. And call Studio E Architects to assist!